Designing a Remote Pressure Monitor for the Unitank
One of the really nice features of the SS Brewtech Unitank is that you’re able to ferment, lager, carbonate and package your beer using only one vessel without the need for transferring to other vessels.
Especially during the carbonation phase you need to keep a close eye on the pressure to be able to tell when the beer is ready for bottling. Normally I dial in the spunding valve when the fermentation is getting close to final gravity and then let the yeast produce the most of the CO2 in the beer. Then once fermentation is done I use force carbonation to get it to the right carbonation level. Carbonation is governed by Henry’s Law, which states:
“At a constant temperature, the amount of a gas that dissolves in a liquid is directly proportional to the partial pressure of that gas in equilibrium with that liquid.”
On other words, as the pressure above the beer increases some of the CO2 is dissolved into beer. This doesn’t happen instantaneously, so most often you apply a higher CO2 pressure to the tank to speed things up a bit. Generally there are two methods for this:
- The fast method (or Crank And Shake), where you apply as high pressure as possible (approximately 2 bar) for a short time. You need to get the timing right, otherwise your beer will get over-carbonated. This method will typically get your beer carbonated in 1-2 days. Since you usually also need to gently shake the vessel to speed the process up, it isn’t really suited for unitanks. The pressure needed is also very close to the maximum pressure of the SS Brewtech tanks.
- The slow method (or Set And Forget), where you apply a head pressure at (or slightly above) the equilibrium pressure. This typically takes 1-2 weeks, but it is nearly impossibly to over carbonate your bear – as long as you have calculated the pressure correctly.
So far I have only used the slow method as it is the most suited for unitanks. In order to calculate the needed pressure, I just type in the temperature and the desired volumes of carbonation in Brewfather and it will provide the needed pressure.
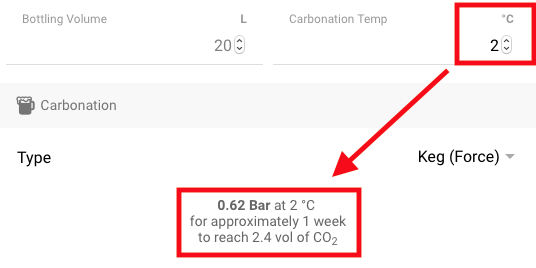
You can also find various force carbonation charts around the internet.
But Why do You Need to Build a Pressure Monitor?
There are a couple of answers to that question. The short ones are “Why Not?” and “Because I Can!”. The longer ones goes more along the line of being able to monitor the progress of the carbonation and being able to determine when the equilibrium pressure is obtained.
It is possible to calculate the exact CO2 pressure needed to produce the desired carbonation level in the beer. But it requires you to know the vetting pressure of the carbonation stone and also calculate the head pressure for the stone, which is determined by the amount of beer above it. For a 7 gal Unitank the last value does not really add that much to the needed pressure, but it will for higher tanks. These two values need to be added to the desired pressure in the tank to reach the right amount of carbonation.
Another reason for me is that the first time I used the Set and Forget method I spent more than 1 kg of CO2 on a 20 liter batch which should not need more than 50-100 g. It turned out that I probably have a tiny leak in one of the connectors. It isn’t big enough that I can detect it during the inspection with soapy water, but it was certainly big enough that it made that first batch of beer fairly expensive to carbonate.
Therefore I have now changed to a method where I turn up the CO2 regulator pressure to 0.2 – 0.3 bar above the carbonation pressure and let it rise until the pressure in the tank is at the desired pressure. Then I let it sit for some time until the tank pressure has dropped a bit again. This usually takes between a couple of hours to a day or two depending on how close to final level the beer is.
This is a quite tedious process, so I have therefore decided to design a system where I can monitor the pressure remotely with just a look on my smartphone or a web browser.
The Initial Design Thoughts
Since I already have a setup with a Raspberry Pi that connects to the Tilt Pi for monitoring the fermentation I want to build something that runs one the same Pi.
I have also made some initial tests that shows that it is possible to log the pressure in Brewfather directly from a Node RED flow. I manually entered the tank pressure read via my “Eyeball Mk I” sensors into a simple flow that sent these measurements to Brewfather as a Custom Stream.
I found a few minor issues with the Custom Stream in Brewfather, but as usual Thomas Gangsøy, the author of Brewfather, was very fast to fix the issues I reported. This is another reason I can highly recommend Brewfather as your primary brewing software.
Besides the integration with Brewfather and Tilt Pi, I am planning on using an analog pressure sensor mounted in some sort of a tri-clamp flange on the unitank. My idea is to put this next to the spunding valve sitting on the overflow pipe. That way I don’t have to worry too much about the sensor getting in contact with the beer.
Finally I’ll need to find a suitable Analog-to-Digital converter that can convert the pressure reading from the sensor into something that can be processed in Node RED.
The initial thoughts and design of the pressure monitor setup can be seen is this sketch:
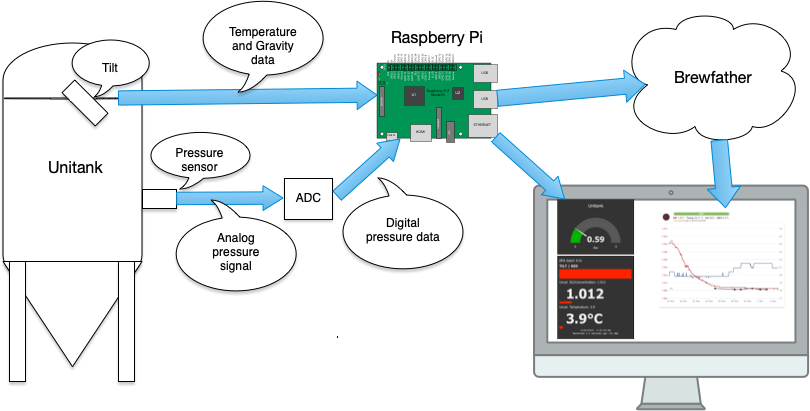
The next step will be to find some suitable components and putting these together. I’ll cover that in a later post.
Hope you liked the post. If you have any questions or comments please let me know below.
2 Replies to “Designing a Remote Pressure Monitor for the Unitank”
That’s another amazing one. Thank you for your inputs.
We will be able to control the “pressure release” at the fermentation stage with this as well, right? 😉
Cheers
Marcelo
The setup I have made is only a pressure monitor. I dial in the release pressure manually on my spunding valve.
But I guess it should be possible to expand it with some remote controlled actuator that allows you to remotely set the release pressure. I haven’t looked into this though, but would be happy to hear about your project. Just remember to keep the PRV on your tank as a simple coding bug might result in an exploding tank.